As emission regulations tighten up and diesel gets more biocontent, Nigel Calder warns of potentially dire consequences for new yacht engines
Reasons to be paranoid about diesel
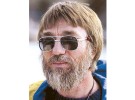
Nigel Calder is best known for his comprehensive Boatowner’s Mechanical and Electrical Manual
In recent years, many sailors have expressed concerns to me about their vulnerability to unrepairable-at-sea engine failure, about electronic control systems, and about high-pressure common rail (HCPR) injector systems and other modern engine technologies landing on our yachts. My response has been that there is no need to be concerned, as we have had this kind of technology in our cars for years.
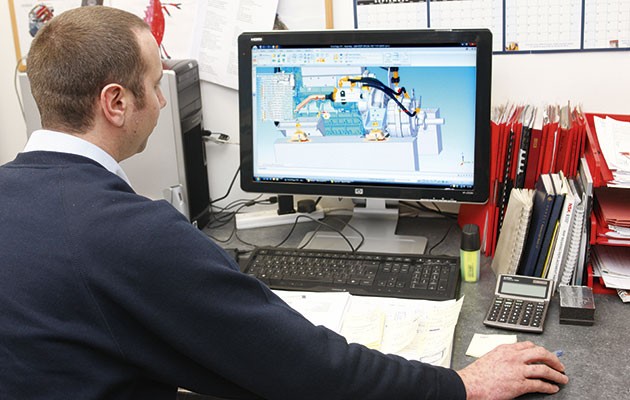
Engine design and evolution may cause problems for boat owners in the future
I’ve come to realise, however, that the core issue is not the electronics but the extraordinarily high fuel system pressures in combination with inconsistent fuel supplies. There are millions of HPCR engines in service in cars and trucks, which would suggest there is no problem, but given the incredibly tight tolerances necessary in the fuel supply, sailors are peculiarly vulnerable because we take on fuel from many different places all over the world with variable cleanliness and chemical properties and we then frequently let this fuel sit in our tanks for months, and sometimes years, at a time.
How did we get here?
Progressively stricter emissions regulations over the past couple of decades have driven, and continue to drive, radical changes in diesel fuel supplies and in diesel engine fuel injection technology. These changes have profound consequences for boat owners now and in the future.
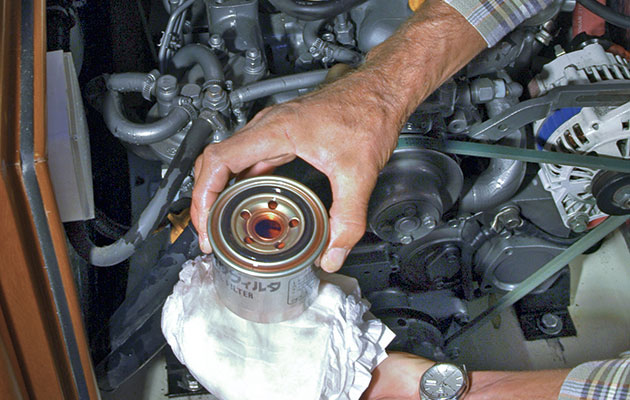
A typical secondary filter (supplied by the engine manufacturer) on a small marine diesel. Without extra primary filtration, this is completely inadequate for cleaning up the fuel supply and protecting the engine
The rapid pace of change is producing some unforeseen side effects (including the Volkswagen emissions test cheating scandal). In particular, changes in the chemistry of diesel fuel and the nature of injection processes are creating challenges for the fuel distribution and filtration industries which are not always well met, and which have outpaced the ability of regulatory agencies to keep up. The result is a significant, and potentially expensive, vulnerability for end users, especially for boat owners with new diesel engines.
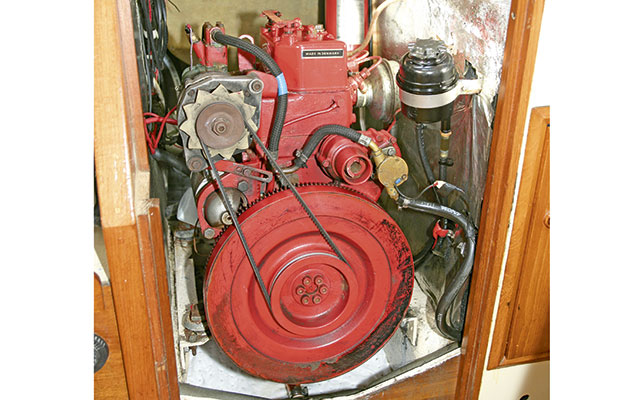
Older engines still need clean fuel, but not to the level of HPCR systems
At one time, diesel fuels contained up to 40,000 parts per million (ppm) of sulphur. Starting in the 1990s, allowable nitrogen oxides (NOx) and particulate matter (PM) emissions for road vehicles were progressively lowered. The new emissions levels could only be met with exhaust after-treatment systems that would be damaged by even small amounts of sulphur, so sulphur limits were steadily lowered to 10ppm – what is known as ultra low sulphur diesel (ULSD).
Unfortunately, the process of removing sulphur from diesel fuel reduces its lubricity (lubrication properties, which are essential to injection pump and injector life), reduces the fuel’s shelf life, removes inhibitors to biological growth, and increases the likelihood of paraffin wax formation in colder weather (the wax then plugs fuel lines and filters). Various additives are put into ULSD to restore the lost properties. Collectively, these are known as surfactants.
In recent years Europe has been introducing biodiesel into the fuel supply, currently requiring 7% (although implementation is variable among member states and is, in general, lagging). Typically, biodiesel is blended with petro-diesel at concentrations between 5% (B5) and 20% (B20). Most engine manufacturers will now guarantee conventional injection systems with B20 biodiesel but may limit high-pressure systems (see below) to B5.
Downside of biodiesel
Biodiesel has significant benefits compared to petro-diesel, notably lowered exhaust pollutants and better lubricity. But then there’s the downside, including reduced efficiency and power, more cold-weather clogging, and greatly reduced shelf life – most engine manufacturers recommend not storing B20 beyond 90 days from the date of production and 100% biodiesel beyond 45 days. It also has increased solvent properties, which will attack some rubbers in older engines and will break loose ‘gunk’ from older fuel systems that have been operating on petro-diesel, resulting in multiple clogged filters. It has a higher retained water content, which promotes corrosion of fuel injection equipment and microbial growth, and there’s a greater risk of injector nozzle coking and plugging, and high surfactancy (more on this also below), none of which is good news for us.
HP injection systems
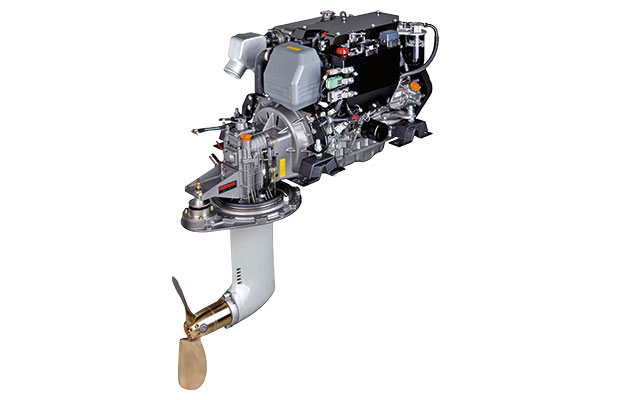
The latest generation of Yanmar’s 4-cylinder engines all use high-pressure common rail injection systems
One of the responses to ever tougher NOx and PM emissions limits has been the introduction of high-pressure fuel injection systems, notably HPCR, in ever lower horsepower engines. The latest generation of small (40hp or more) Yanmar four-cylinder engines are now HPCR. Whereas the pressure in conventional injection systems rarely exceeds 5,000 psi (350 bar), it is not uncommon to see 30,000 psi (2,000 bar) on HPCR engines, with some as high as 40,000 psi (2,700 bar). Predictions are that pressures may go as high as a staggering 60,000 psi (4,000 bar). These kinds of pressures require orifice sizes, clearances and machining tolerances to within 1-3 microns, where a micron is a millionth of a meter. To put this in perspective, a human hair is around 80 microns thick; the human eye can detect objects down to about 40 microns.
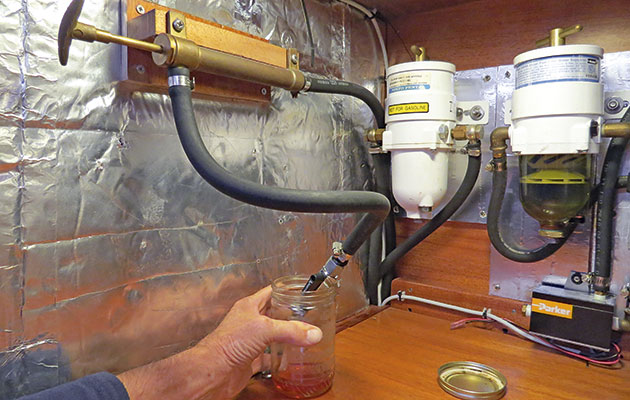
Nigel’s fuel sampling pump, used to take a sample from the base of his fuel tank after refuelling
Fluids at these pressures are capable of acting like water jet cutters, especially if there is even microscopic hard particle contamination in the fuel. The result is scoring and abrading of critical injection pump and injector components. For conventional (low pressure) fuel injection systems the critical particle size to initiate abrasive wear is about 6-7 microns. With HPCR injection, the critical particle size is approximately 2-3 microns. Absolute fuel cleanliness is essential to engine life.
Inadequate standards
As long ago as 1998, engine manufacturers developed the Worldwide Fuel Charter (WWFC) to define minimum diesel fuel cleanliness levels based on a European standard, ISO 4406. But even if fuel supplies from a refinery meet the ISO standard, typical contamination levels in fuel tanks and at primary filters have been found to be ten times higher than the ISO target. In point of fact, HPCR engines require a fuel cleanliness at the injection pump and injectors that is up to one hundred times lower than the ISO target and one thousand times lower than common tank contamination levels in the real world. This represents a major challenge for the fuel filtration industry.
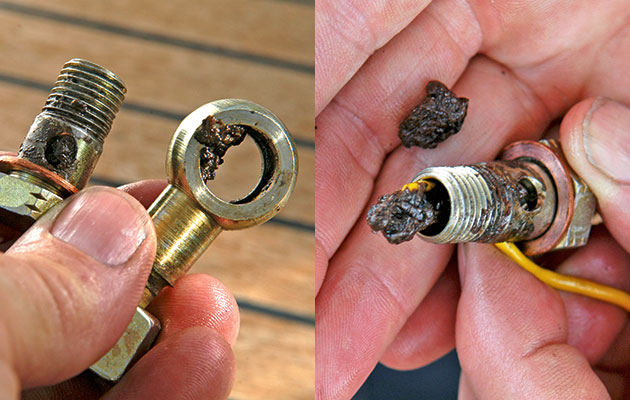
This fouling in Nigel’s own fuel system was caused by the solvent properties of biodiesel, which dissolved ‘gunk’ out of a fuel-supplier’s tank and completely plugged the suction line and primary filter
Traditional fuel filter elements are not adequate for HPCR systems. What is more, the filtration industry does not currently have particle counters (or laboratory test dust) suitable for calibrating instruments below 4 microns – in other words, the smallest particle detection and counting level is above the size of the most damaging particles for HPCR systems! Discussions are under way to, among other things, revise international standards to account for particles down to 1.5 microns in diameter.
The ISO test procedure for filters is a multi-pass test, in which the fuel is recirculated through the filter over and over. This is more appropriate for hydraulic systems than it is for diesel fuel supplies and engines. It uses hydraulic oil, which is far more viscous than diesel fuel. Also, the test does not account for vibration and sudden changes in engine speed, both of which have been found to cause rapid and considerable increases in the number of contaminants of a given size passing through a fuel filter.
Water in the fuel
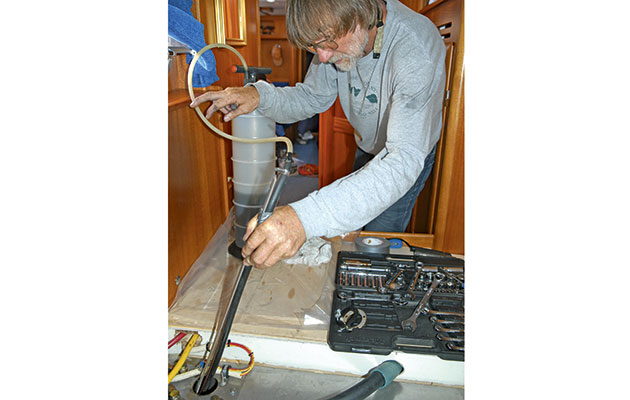
Nigel accessing his fuel tank to pump out contaminated fuel
Problems are compounded by the surfactancy of the additives to ULSD, and by biodiesel’s natural surfactancy. One of the main purposes of most primary fuel filters is to remove any water from the fuel supply. Unfortunately, the increased surfactancy of ULSD and biodiesel reduces water droplets to a size at which a high percentage of the droplets can pass through conventional separation media.
The bottom line: diesel fuel that meets current supply chain and WWFC standards, fed through filters that pass the relevant tests, can threaten the health of modern fuel injection systems. To meet fuel cleanliness targets with HPCR engines, multiple-stage filtration at the two-micron level may be needed.
Paranoia recommended
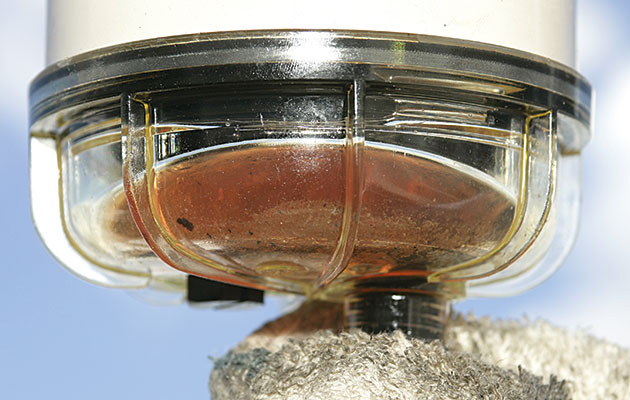
Even minor contamination like this could wreak havoc if it made it to the high pressure side of the engine
The situation is likely to improve over time. Upcoming changes in emissions and engine efficiency standards, in particular the forthcoming Euro 7 requirements for automotive diesels, will lead diesel engine manufacturers to demand higher-efficiency filters that will then find their way into marine and aftermarket filtration systems.
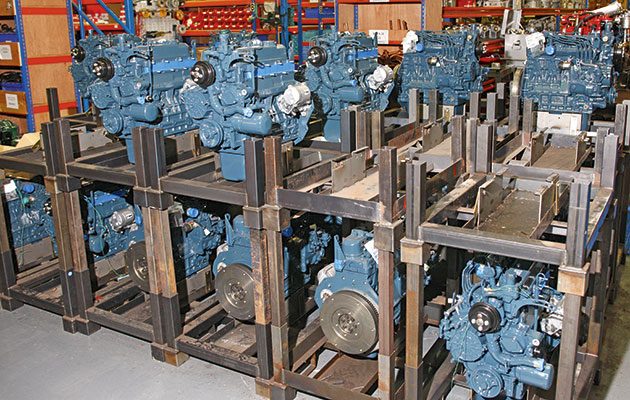
Not all new diesel engines are HPCR. These Kubota engine blocks, awaiting marinisation by Beta Marine, still use conventional technology
Nevertheless, it will take some time for the effects of changing emissions and fuel filtration standards, and engine manufacturers’ requirements, to have a practical impact in the marine filter marketplace. In the interval, anyone with a high-pressure injection system should be somewhat paranoid about the quality of fuel supplies and the level of filtration being provided for the engine.