Duncan Kent explains how to prevent electrochemical corrosion causing rapid and significant damage to your boat
One of the most worrying things that can happen to a boat owner is to discover vital and expensive metallic underwater items such as propellers, prop shafts and saildrive legs are actively dissolving or being eaten away for no apparent reason.
But there is a reason, of course, and that’s the unwelcome phenomenon of electrochemical corrosion, of which two main types can affect your yacht: galvanic corrosion and stray current. Although similar in their often catastrophic outcomes, the causes of the two are entirely different – as are the cures.
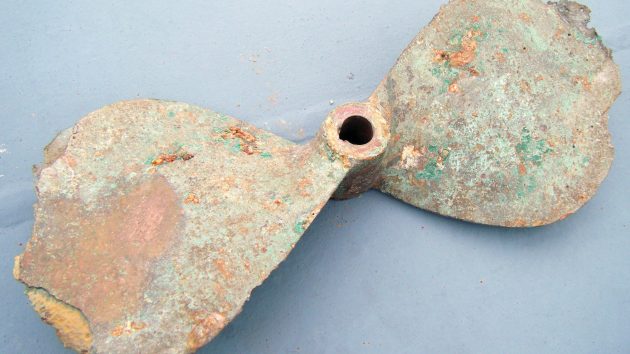
Propellers are particularly vulnerable to galvanic corrosion
Galvanic corrosion
Galvanic corrosion (GC) is a reaction between two or more different metals when submersed in a conductive solution (electrolyte), which, in the case of boats, will be salt or fresh water. Some metals are more vulnerable (less noble) to corrosion than others, and the process of GC is where the least noble metal becomes the anode, causing the electrons to flow to the more noble metal, the cathode. This converts the atoms in the anode into ions, which dissipate into the electrolyte. GC can only exist where there is a closed electrical circuit: that is, where the two metals are physically touching or linked together electrically by a conductor.
So, if you electrically connect a piece of steel and a piece of zinc together and immerse them into the same electrolyte (seawater, for instance), you will create a galvanic cell (in effect a battery) in which electrons will flow from the zinc (anode) to the steel (cathode), causing the zinc to corrode before the steel.
The speed at which the least noble metal deteriorates is determined by the difference in the nobility of the metals, the type of electrolyte in which it is submerged, and the relative surface areas of the anode and cathode. The latter is important because for each positive ion released at the anode, electrons in the cathode form a negative ion in the electrolyte to equalise the situation. This ‘one for one’ process means that if the anode is larger than the cathode, the anode will corrode more slowly, and vice-versa.
The most common example of GC in boats occurs when you have a bronze propeller on a steel propshaft. The two different metals are physically connected and immersed in an electrolyte (seawater), which naturally causes the least noble metal (bronze) to dissolve unless some form of prevention is established.
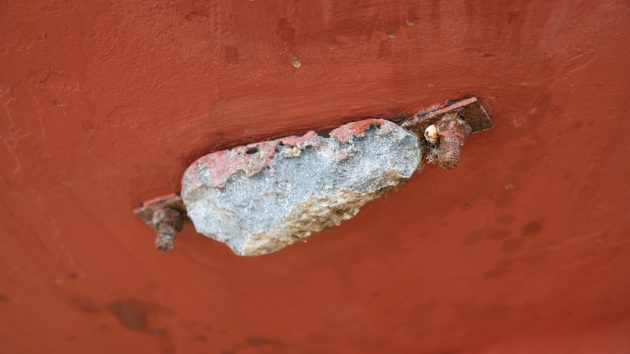
Sacrificial anodes are a boat’s primary protection
Galvanic corrosion prevention
The primary method of preventing galvanic corrosion to the underwater metal parts of your boat is by the use of sacrificial anodes. The idea being that if you submerge another less noble metal in close proximity to the item you’re trying to protect, and then connect them together electrically, then the less noble metal will dissolve before the more noble one.
For boats in seawater the most common anode used is made from zinc, whereas for boats in fresh water it’s magnesium, though aluminium is now also used in sacrificial anodes. For the protection circuit to be complete the anode must be electrically or physically connected to the item it is protecting.
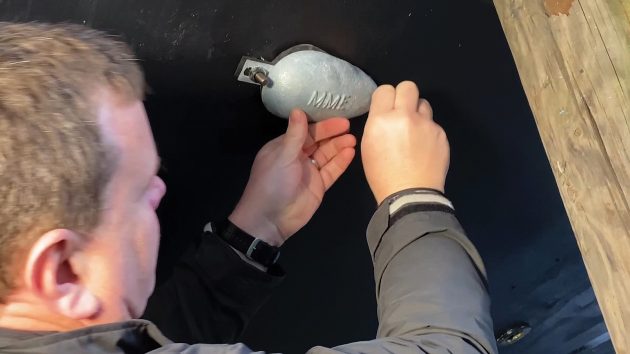
Check all your connections for loose wires and terminals
Bonding
Bonding is always a contentious issue as even the ‘experts’ often disagree.
My own opinion, and that of many professional marine electrical engineers, is that all metallic objects such as engines, drive legs, pumps and skin fittings should all be bonded together using 6mm² wire at least.
All these items should then be electrically bonded to all your sacrificial anodes. It’s also important to ensure that all bonding cables and connections are routinely inspected for insulation wear/damage and/or corrosion at the terminals, especially those made inside the boat’s bilges. It’s also a good idea to test for resistance between an anode and the area of metal it is intended to protect using a multimeter set to the Ohms (resistance) range.
If there’s a high resistance you need to check all your connections for corrosion or loose wires and terminals.
You can fit nylon skin fittings, such as the popular Marelon or TruDesign brands, as being non-metallic and thereby non-conductive, means they don’t need electrically bonding.
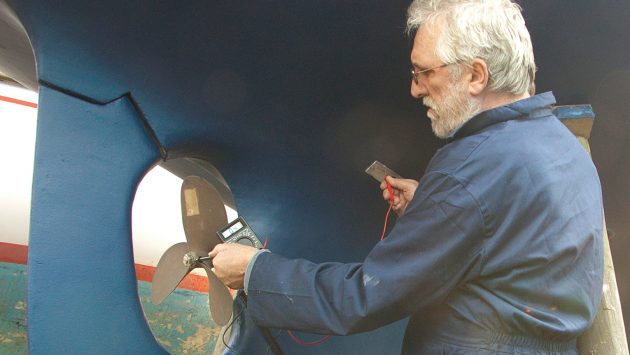
You can assess your yacht’s threat of corrosion with a simple test
Detecting a galvanic circuit
If you have a specific problem with corrosion and want to test whether you have adequate protection against it then you can carry out a simple test. The electrochemical potential of any metal is a small negative voltage that can be measured by using a corrosion reference electrode connected to a digital multimeter. The most common electrode used for testing is a silver/silver chloride electrode, which is basically a silver wire coated with silver chloride.
This electrode should be immersed in the water, near to the metal you’re concerned about and connected to the positive probe of your meter. The negative meter probe should then be connected to your boat’s negative (battery negative or bonding circuit).
The multimeter is then set to the millivolt setting and the display reading noted. This reading is known as your ‘hull potential’. If your anode protection is working this figure should read no less than -200mV (avg. -550mV in salt water) but might read up to -1,100mV depending on the makeup of the water. Less than -200mV indicates your anodes are not working efficiently.
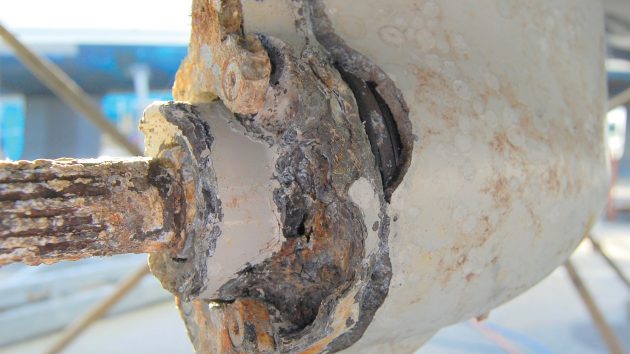
Corrosive damage caused by stray current while the boat was connected to shore AC power
Stray current corrosion
Similar to GC but caused by a different set of conditions is stray current corrosion (SCC), which can only occur when you are connected to shoreside AC (alternating current) power. Put simply, SCC is a process of electrolysis caused by the presence of an external electrical current, whereas GC is caused by a variation of electrical potential between dissimilar metals.
The notable difference is that in GC the voltages are limited and small, whereas with SCC they can be unlimited, so that the damage inflicted can be much more significant and take effect more rapidly than with GC. Furthermore, the amount of corrosion is directly proportional to the magnitude of the stray current at the point of discharge.
For safety reasons, the shore supply’s AC earth should always be bonded to your vessel’s own grounding circuit, which in itself will be connected to all of the metallic components on board including the engine, propshaft, saildrive and skin fittings.
SCC occurs when an electrical current flows through any metal fitting that is immersed in the surrounding water which, in effect, is ground. This can quickly cause the metal to corrode, particularly in more ‘anodic’ metals such as aluminium. It’s the reason you sometimes hear of boats where the saildrive leg has literally ‘dissolved’ in a matter of just a few weeks.

An in-line galvanic isolator is highly effective and simple to plug in
Stray current prevention
The best way to stop stray current corrosion is by disconnecting the earth link to your shore power connection. Obviously, you wouldn’t want to do this while keeping the power connected as there would be no path for dangerous electrical leakages to dissipate safely. So, the only solution is to find a way for the connection to remain for large AC fault currents, while stopping the smaller DC currents from flowing.
The simplest and cheapest method is to fit a Galvanic Isolator (GI), sometimes called ‘zinc savers’, which is a small device that fits into the shore power earth circuit, on the shore side of the consumer unit (CU), that contains your circuit protection including a Residual Current Device (RCD) and circuit breakers.
The simplest GIs come ready wired with a plug and socket that you just plug into your boat’s shore power inlet and plug the shore power cable into the socket on the GI cable. Others require you to break into the shore power lead and cut the earth wire before reconnecting it via the terminals on the GI box, which ideally needs to be mounted under cover.
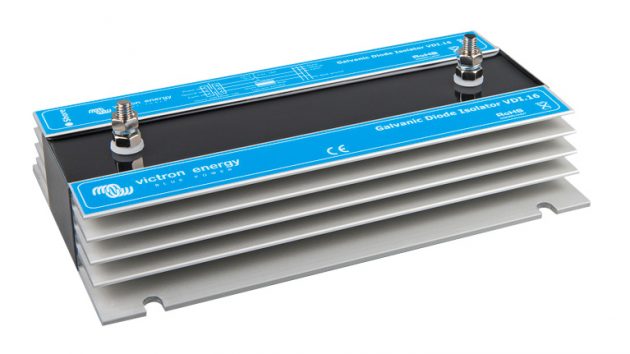
A good galvanic isolator will protect your yacht for not much more than £100
Whichever you choose, the GI should always be failsafe (default to dead short), so that in the event of diode damage from a high-current AC surge, you will always retain continuity of your earth. A better alternative to a GI is an isolation transformer (IT), which will entirely isolate your boat’s own AC system from the shore supply. The only downside of an IT is that they are expensive, bulky, very heavy and sometimes a little noisy.
For these reasons they are rarely fitted to small or medium-sized coastal cruisers. I would, however, strongly recommend you install one if you’re planning on cruising to areas where the integrity of the electrical supply is uncertain.
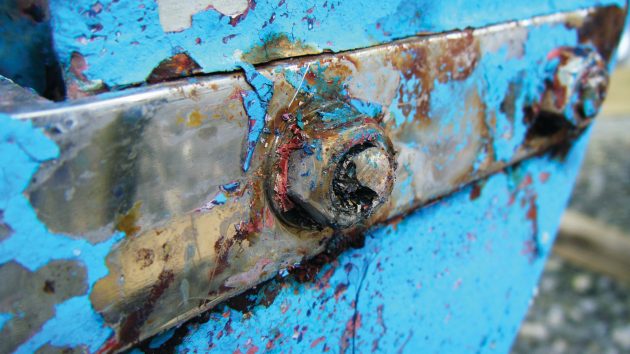
Example of metal crevice corrosion, where moisture can get in, stagnate and then lead to the corrosion even of stainless steel
Crevice corrosion
Another form of corrosion that affects many metals, particularly stainless steel, is called crevice corrosion. A crevice is most commonly found where moisture can get in but not back out, creating an area of stagnant water containing little or no oxygen. Stainless steel is a steel alloy containing chrome and nickel, which gets its ‘stainless’ characteristics from a thin outer skin of chromium oxide. If deprived of vital oxygen this skin breaks down, leaving the steel to corrode as if it were just plain mild steel.
This effect can often be seen when plastic covers are put over rigging turnbuckles, allowing seawater to get in but not enough air to provide the oxygen needed to keep the metal ‘stainless’.
Although galvanic activity is often a cause in crevice corrosion, microbial corrosion (AKA: biocorrosion) is another common factor, particularly when occurring in steel boats, and is often the cause of oxygen depletion leading to hydrogen sulphide build up in oxygen-depleted crevices.
The only way to prevent crevice corrosion from forming is to get rid of the places where moisture can collect and stagnate. For instance, the addition of non-porous washers, gaskets or backing plates to areas like hull/chainplate fixings. Or simply by sealing areas off using a waterproof sealant.
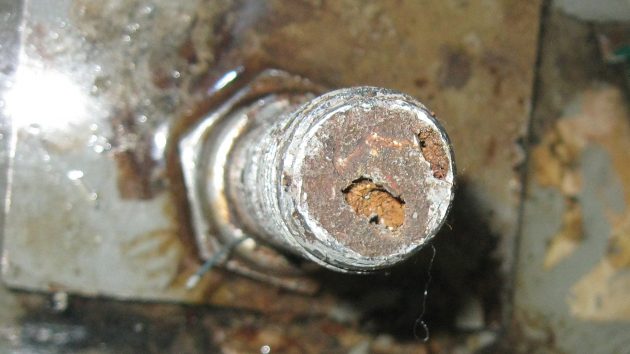
Water droplets produce galvanic cells that can eventually penetrate metal
Pit corrosion
This is where tiny galvanic cells are created by droplets of water left on the surface of a piece of metal, forming a small corrosion pit. If left these can grow, penetrate the metal and cause greater problems down the line if that item is part of an important structure. Typical examples of this are rigging chainplates, turnbuckles, deck plates, window frames, etc. Any metal, in fact, that is prone to getting covered with seawater spray when sailing.
The simplest and most effective way of preventing this is by regularly hosing your boat down with fresh water after a trip out. Once dry, there are numerous types of coatings such as Lanocare that can be applied that will encourage the salt water to simply run off rather than remain in droplets on the surface of the metal.
Electrolysis – surveyor’s advice
Electrolysis used to be called ‘nail rot’ on wooden boats, but I’ve seen it several times on GRP yachts I’ve surveyed. Electrolysis changes the ions in the carbon rich fibreglass, causing it to soften around metal skin fittings or anode fixings. GRP is an ionic substance, as is wood, except in wood the de-ionisation around iron nails is more obvious.
The copper in Coppercoat and other copper rich antifoul coatings conducts electricity and causes the GRP hull to de-ionise and degrade around metal skin fittings that are bonded to anodes. This is a rare example of when bonding to anodes can be harmful.
Another concern is boats with aluminium rudder stocks. In one yacht I surveyed the aluminium stock had reacted with the copper in the antifouling, causing the rudder stock to corrode and expand. You must bond an aluminium rudder stock to a hull anode, and you need to keep copper-based antifouling well away from it.
When it comes to the bonding of anodes, metal items to be protected need to be in line of sight of the anode, even if they are electrically bonded by wire. Furthermore, anodes are only effective at a distance of up to seven times the length of the anode from the object. They don’t work if too far away and/or out of sight.
Another consequence of electrolysis is hydrogen sulphide gas. When metal corrodes the metal oxides use up oxygen and turn the air into hydrogen sulphide, and, consequently, the bilge water into sulphuric acid. Hydrogen sulphide – a colourless gas – is lethal, so if you smell rotten eggs inside a steel boat you need to investigate the source immediately.
Enjoyed reading this?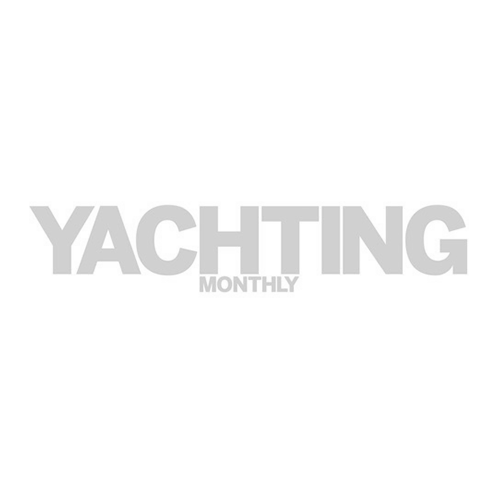
A subscription to Yachting Monthly magazine costs around 40% less than the cover price.
Print and digital editions are available through Magazines Direct – where you can also find the latest deals.
YM is packed with information to help you get the most from your time on the water.
-
-
- Take your seamanship to the next level with tips, advice and skills from our experts
- Impartial in-depth reviews of the latest yachts and equipment
- Cruising guides to help you reach those dream destinations
-
Follow us on Facebook, Twitter and Instagram.