Considering changing you boat rigging to composite but confused by the options? Sam Fortescue takes a look at the pros and cons of various solutions
‘Like the shift from wooden spars to alloy spars after the Second World War, we are moving to carbon spars and composite boat rigging for cruising boats,’ says well-known surveyor Kim Skov-Nielsen. ‘We are living on the cusp of a major shift to all-composite rigs.’
Four broad options for modern boat rigging run from ultra-high molecular weight polyethylene (HMPE) to aramid, PBO (poly-benzoxazole) and finally full carbon.
Compared to steel, all these options offer much lighter weight, which makes for less pitching and rolling in a sea. Greater rig stiffness improves sail trim and transfers forces more efficiently – particularly in lighter winds. And synthetic fibres resist the invisible fatigue that undoes stainless steel systems.
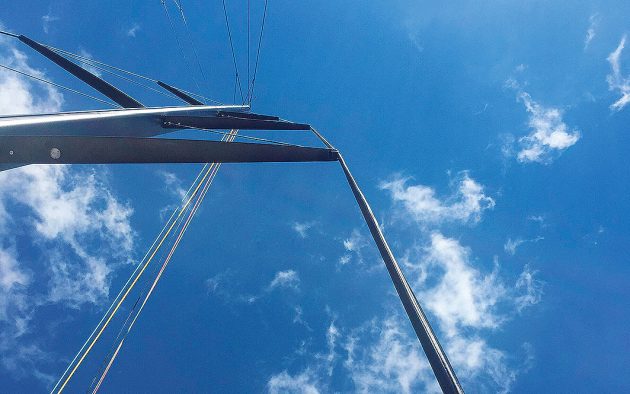
For budget-conscious boaters looking to save weight aloft, carbon rigging is a much cheaper way to do it than carbon spars
On the other hand, the cost can be two to four times that of wire boat rigging, and repairs are tricky outside major sailing centres. Some of the fibres degrade rapidly with exposure to UV or moisture, so damage to the sheathing will shorten the lifespan of the stay.
Carbon in particular is also susceptible to impacts from the side. Every sailor will weigh up the options differently, but here are your choices:
HMPE (Dyneema/Spectra)
Dyneema and Spectra has extraordinary tenacity and a very low weight, but many riggers are wary of using it on cruisers because they consider it too elastic.
However, US specialist Colligo Marine says it is just a question of picking the right grade of Dyneema and sizing it correctly. ‘Many people have mistakenly sized Dyneema for break strength and ended up with a very stretchy rig,’ says John Franta of Colligo Marine. ‘Stretch is a function of cross-sectional area, so all you need to do is pick the right diameter for your application.’
That means you’re going to end up with a bigger Dyneema line than your original wire, causing marginally more windage, albeit at a fraction of the weight. For example, the 8mm wire that is standard on many 40ft cruisers would have to be replaced with 11mm Dyneema in a Colligo Dux system, but this should creep less than 3mm per year.
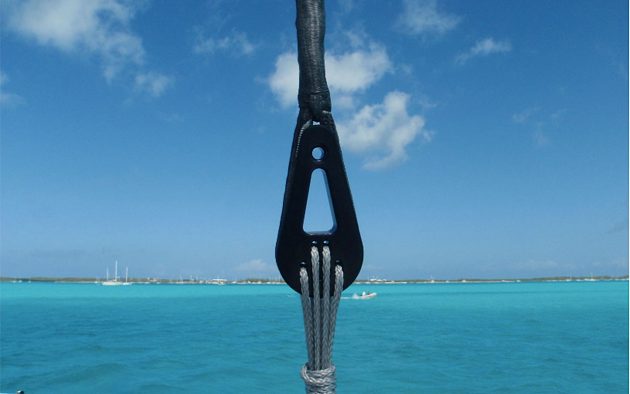
Colligo’s aluminium chainplate eye can be tensioned with a lashing on sub-30ft boats
The variety of HMPE you use is vital, too, as the strands within the line align themselves with the load.
‘A 50ft-long backstay made from normal Dyneema can grow 4-6 inches in length,’ says Franta. That’s why Colligo only uses heat-stretched Dyneema SK75, where the fibres are already very tightly aligned, instead of higher-tech grades like SK99 and DM20.
A typical HMPE stay is spliced around a lightweight aluminium thimble, which fits easily to traditional fork at the deck end. You’ll need a special Colligo stemball fitting aloft or a CheekyTang, spliced into a loop at the top end of the shroud, then bolted through the mast.
Chafe and UV are the chief enemies of Dyneema rigs. ‘It is easier to cut and has a low melting point of 100°, so a fast-moving sheet could cut through it in seconds,’ warns Marlow sales director Paul Honess. Colligo is PVC shrink-wrapped for this reason and should last eight to 12 years without mishap.
Aramid
Aromatic polyamides (Kevlar is a Dupont trademark) have low creep and high tenacity, but they also resist abrasion well – important when pitching and rolling across the Atlantic, for example.
Article continues below…
Improving performance through tuning standing rigging
To tune or not to tune? Would you drive your car with wheels misaligned? Run a marathon with your shoelaces…
How to check your rigging – video guide
A screwdriver, a straight edge and a good set of eyes are all that’s required for a basic rig check.…
Aramids are five times stronger than steel rope weight-for-weight, but that multiple falls if the fibres become wet and UV light causes them rapid damage, so cables have to be well sealed and protected.
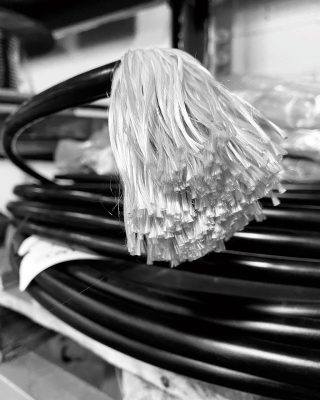
Aramid stays
OYS has been designing Kevlar backstays with stainless steel terminations for years, and recommends a maximum working load of 40% of the cable’s breaking strain to minimise creep, so aramid stays are a little fatter than rod equivalents.
For example, an 8.5mm cable can take loads of 3000kg and yet weighs just 60g per metre. Compare that to Nitronic, where 7.5mm rod offering the same working load weighs 350g per metre. ‘You size it for stretch, and then you end up with a much higher safety factor,’ says Robbie Sargent of OYS. ‘It’s flexible and you can coil it up, plus it’s relatively price competitive and looks smart. Aramid is to all intents and purposes a cruising product.’
Black sheathing is standard, but lighter custom colours can reduce the cable’s resistance to UV. OYS does not recommend aramid shrouds on a monohull. ‘Rod and wire is pretty bullet-proof in terms of chafe and physical damage,’ says Sargent. ‘Composite rigging is a lot more fragile. A mid-sized Oyster or Swan has full battens – can go that goes through the textile sheath very quickly.’
The material works well in fore- and backstays, runners and inner fore-stays, or as lateral rigging on a multihull, he adds.
Dutch-based Aramid Rigging uses an advanced endless winding machine for made-to-measure stays. The bundle of fibres is in turn wrapped in heat shrink to keep out water, then an outer protective braid with a UV-resistant coating. The metal thimbles at each end are then sealed inside a polyurethane moulding, eliminating one common point of failure for steel rigs.
PBO
Developed in the 1980s, polybenzoxazole or PBO was seen as a step up from aramid for rigging raceboats, with nearly twice the strength and modulus – stiffness. It weighs less than 20% of rigging wire, and manufacturers have developed an easy-to-fit cruising product.
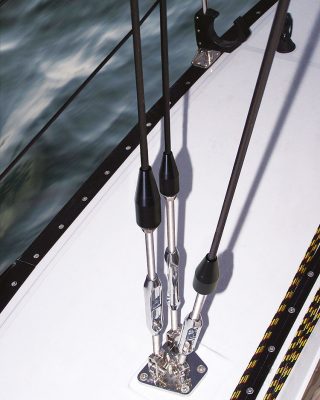
Powerlite PBO cables from Applied Fiber
Westmarine in the US worked with Applied Fiber to develop the Powerlite brand – fully compatible with normal terminations at the mast and deck, so it can be swapped for an existing wire or rod stay.
A sheath is extruded on to pre-tensioned bundles of PBO at the manufacturing stage, protecting the fibres from UV, water and abrasion. It can even be run through the spreaders like steel.
Allspars is the UK supplier for the Dutch EasyRigging system, but both manufacturers agree the rig should be replaced after eight years – sooner if the boats have been raced hard. Babystays, runners and removable forestays should be replaced after just four years. Some riggers, however, say that PBO has been eclipsed by carbon for performance, while Dyneema and aramid stays are cheaper and more robust. ‘PBO has proven unreliable, inexplicably brittle and very susceptible to UV damage,’ says surveyor Skov-Nielsen. ‘It doesn’t even get discussed these days when contemplating new rigging.’
Carbon
The state of the art remains carbon, where Future Fibres dominates. Before you turn the page with a scoff, know that costs have plunged and manufacturing has improved – bringing carbon rigging within reach of cruising boats.
‘ECthree is entry-level for those that want to move away from rod rigging for better performance and more comfort at sea,’ says general manager James Austin. ‘We have a mission to democratise that and make it a more accessible product for someone in the 30-60ft category.’
ECthree is made of rods of pure carbon, bundled, sheathed and fitted with stainless steel terminations, making them easy to retrofit. It is similar to the peak performance ECsix product. ‘It is 20% lower in modulus but one fifth of the cost,’ says Austin. ‘We think that’s a good compromise.’
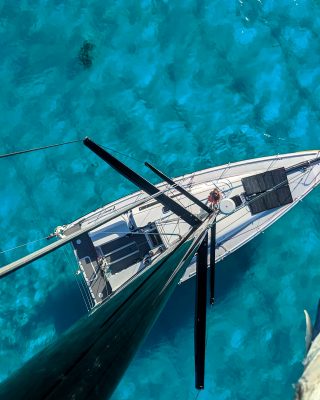
Moving from rod to carbon rigging on a 45ft yacht is ‘equivalent to having an extra person sitting on the rail’
Carbon boat rigging saves 65% of the weight of rod rigging. It is invulnerable to water or UV, so is ideal for use on a yacht. True, carbon doesn’t handle lateral forces as well as steel, but the construction allows the fibres to move and flex within the sheath.
The stainless-steel fittings are designed to be replaceable, but the cable should be inspected and serviced regularly – a service Future provides in the package.
‘It is unrealistic to think we can get to the same price as rod, but we would hope to be less than double,’ says Austin. ‘It’s undoubtedly a cost premium to have composite rigging, but you have to look at it over 15- to 20-year life-cycle of the boat.’ The lateral rigging on a Grand Soleil 46 refitted recently cost around £15,000.
LightSpeed, a smaller US manufacturer that is also trying to drive carbon rigging into the sub-80ft cruising bracket, uses the same Toray T700 as Future, with smart titanium terminals that fit most common types of standard rigging screw and mast fitting. ‘We are unique in building an integrated Technora blend into the hoop structure of the cable, which delivers unmatched cable chafe protection and durability without adding bulk of a cover,’ says technical specialist Mike Wasten.
Comparative boat rigging costs
- Wire and rod – rigging a Dehler 38 with standard 1×19 wire or Nitronic rod, would be an estimated £2,280 for wire and around £5,000 for rod.
- HMPE (Dyneema/Spectra) – Cables to rig a Dehler 38 would cost £2,900-3,700.
- Aramid – costs of around £7,500 for the Dehler 38 are 40-60% more than rod rigging
- PBO – Powerlite claims its cables cost just 30% more than rod, quoting $8,525 (£6,210) for a Dehler 38 with running backstays.
- Carbon – $20,000 (£14,600) for a complete set of stays with runners to suit a Dehler 38.
Enjoyed reading this?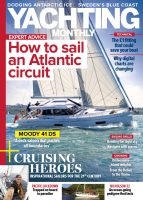
A subscription to Yachting Monthly magazine costs around 40% less than the cover price.
Print and digital editions are available through Magazines Direct – where you can also find the latest deals.
YM is packed with information to help you get the most from your time on the water.
-
-
- Take your seamanship to the next level with tips, advice and skills from our experts
- Impartial in-depth reviews of the latest yachts and equipment
- Cruising guides to help you reach those dream destinations
-
Follow us on Facebook, Twitter and Instagram.