Sam Fortescue shines a light on boat building jargon and looks into a future devoid of fibreglass
The end of GRP? Sam Fortescue looks at past, present and future boat building materials
Glance at a brochure for a new boat or walk the pontoons at the Southampton show and you may have come across some terms that didn’t mean much to you.
The art of boat building is as recognisable as ever, but the science of it is constantly developing. New materials and new techniques can make it hard to compare like with like.
Take wood, for instance: the material of boatbuilding choice for millennia.
There are still plenty of wooden boat-builders out there, labouring away in dingy sheds and halls to craft pilot cutters, rowing skiffs and other emblematic vessels of yesteryear.
But perhaps the best known of the wooden boatbuilders is Spirit Yachts in Ipswich, building thoroughly modern boats – in composite wood.
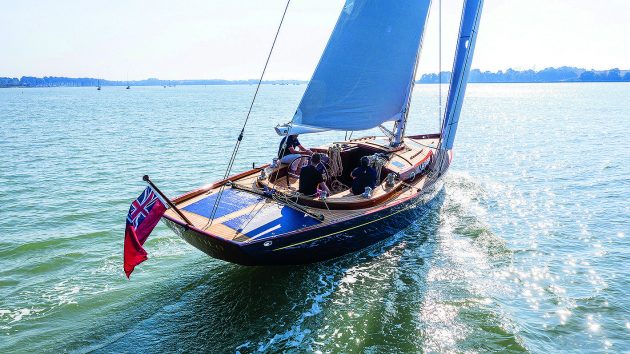
The Spirit 44E is a ‘zero carbon’ cruising yacht. Credit: Richard Langdon
‘Certainly we use epoxy resin to bond the components together, but the amount of resin used is minute compared to GRP or carbon,’ says founder and head designer Sean McMillan.
‘Both carbon-fibre and GRP rely totally on being saturated with a high density of polyester or epoxy resins to impart structural integrity. Wood, whilst also a linear fibre material, is cross-linked with a cellular structure entirely created by nature and has full structural integrity in its own right.’
In fact, the 1.6-tonne Spirit 30 daysailer employs just 73kg of resin and 12.2kg of hardener in its entire construction.
‘In 20 years’ time, when GRP has become socially unacceptable – not to mention any future end-of-life legislation – who knows, we may look back and see the last 60 years of GRP boats as a historical niche,’ finishes McMillan defiantly.
Another example is racy French builder RM Yachts, whose boats are famously swift, with offshore hulls designed by Marc Lombard.
And yet they are built in plywood and epoxy.
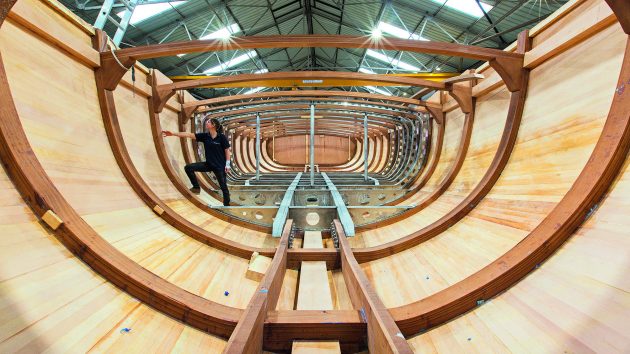
Thought every Spirit yacht us built of wood, it is a composite of glue and epoxy sheathing.
It is flexible, robust and far more sustainable than standard glass-reinforced plastic.
Sheets of laser cut Okoumé plywood up to 22mm thick are bent around a mould and epoxied to plywood structural members.
The whole lot is also epoxy sheathed for longevity.
It’s a technique which means that the brand-new RM 1380 is 9.8 tonnes light – slightly less than the comparable X4-6 from X-Yachts.
‘Plywood is the soul of an RM. It a very useful material, allying a good stiffness with lightness – perfect for building the hull and the structure,’ says head of engineering Edouard Delamare.
‘But plywood is nothing without epoxy, because it ensures the waterproofing – vital in a marine environment.’
Boat building using glass-reinforced plastic
Many series production yards, from Beneteau to Bavaria, still use the most basic form of wet lay-up – splurging resin on to mats of glassfibre with a roller to get them well wetted out before laying down the next layer of glass.
It is very hard to control how much resin is applied and there are often air pockets between layers.
For this reason, hulls built this way tend to be overbuilt and heavier.
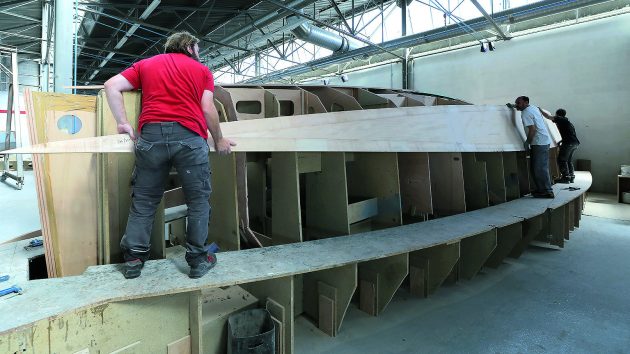
RM Yachts is unique in building its offshore yachts in plywood and epoxy
Polyester is the cheapest and most commonly used resin, but it can bond with water, creating the problem of osmosis.
That’s why isopthalic gelcoats are applied to the outside of the hull, to act as an effective barrier to moisture.
Vinylester creates many more bonds than polyester and is reckoned to be up to three times stronger, but it costs more too.
And epoxy is the best performing resin of all, used only in high-quality lay-ups. All are pretty toxic, and sport the ‘dead-fish’ icon on the side of the tin.
Infusion
When vacuum infusion emerged as an industrial technique in 1990, it allowed boatbuilders to use less resin and spread it more evenly around the finished panel for greater strength.
But it generates a lot of waste, because each infused part has to be prepared with a host of plastic layers.
Besides the plastic of the vacuum bag itself, there’s a breather layer to distribute the resin and a peel ply to stop it sticking to the infused part; a thick bead of sealant tape; disposable feeder tubes are required every few inches, and many of the vacuum tubes must also be binned.
The technology has not stood still, though, and there are now reusable vacuum bags made from inert silicon, for instance.
Some bags have the mesh structure necessary to spread the resin built in, while the aerospace sector has pioneered the use of PTFE membrane that stops resin clogging up the vacuum pump side of the system.
Sweden’s Arcona builds its fast cruisers using vacuum infusion, and has for many years.
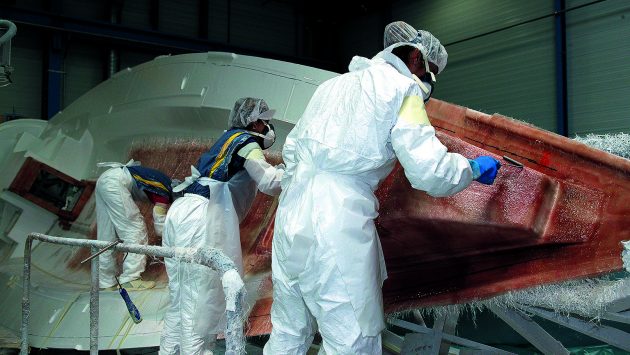
Hand lay-up is a process that has changed little over the years of boat building
But in order to add strength and stiffness, it laminates in a steel support frame amidships to transfer the loads from the rig into the keel.
Improvements in lamination techniques mean that the boats are lighter than ever.
Late Arcona designer Stefan Qviberg said the current Arcona 40 displaced a whole tonne less than its equivalent a decade earlier.
Other boat builders use other types of reinforcing for the high-load areas of the hull.
Aramids like Twaron and Kevlar often feature, as do selective areas of carbon-fibre on stringers and around keel bolts and chainplates.
High-end yacht builder Baltic uses carbon reinforcing, for instance, to add strength without extra weight.
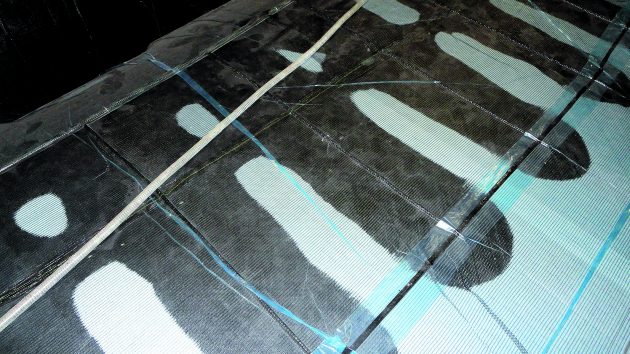
Vacuum infusion uses less resin but creates a lot of plastic waste
Performance catamaran brand Catana likewise uses Twaron and carbon in its lay-up to save hundreds of kilos; some 700kg in the old Catana 47.
Some claim that aramid reinforcing makes a hull safer, for example in the event of collision with a container, but others refute this.
Naturally enough, carbon is still the ultimate performance material because of its blend of strength, stiffness and light weight.
It is also prohibitively expensive relative to other fibres and very resource-intensive to produce, as it requires temperatures up to 3,000º C and a plastic feedstock.
Pre-preg
The bulk and waste of the infusion process has led to another step forward in the form of so-called pre-preg materials, where the sheets of fibre used to strengthen the hull come ready-coated with a pre-catalysed form of the resin that reacts very slowly at room temperature.
Instead of needing to mix epoxy with hardener and reduce its viscosity with toxic styrene to draw into the mould, a precisely-controlled curing process activates and sets the resin.
The result is a stronger, lighter laminate than can be produced through wet lay-up.
Gurit’s SPRINT system goes a step further by sandwiching a thin film of heat-activated resin between two layers of fibre.
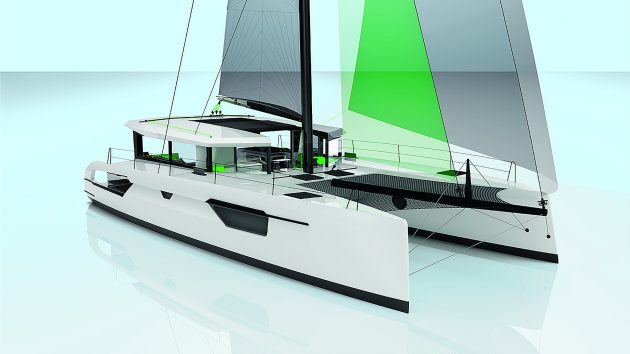
Windelo uses basalt fibre to strengthen its hulls during the boat building process. It is said to be much less carbon intensive than using glass
The advantage of this is that the fibres remain dry until curing so air can be more easily removed under vacuum to produce a laminate with a void content of less than 0.5%.
Baltic Yachts uses this technique, building an oven around its hulls to cure them.
‘With one or two exceptions, we haven’t infused a boat for some time,’ says CEO Henry Hawkins.
‘Using Sprint and pre-preg materials saves weight compared to vacuum infusion. With hand lay-up, generally more resin is mixed than needed and a lot gets discarded. This is the same with infusion where resin is lost or wasted in the plastic hoses and pipes and breather film and within the distribution channels.’
Continues below…
The dirty truth about teak
Teak is beloved by boat owners and shipyards for decking and yacht building, but any claims that it is sustainably…
ON TEST: Spirit 44e – the sustainable future of sailing?
A wooden boat that blazes a trail for modern technology and sustainability sounds too good to be true. Theo Stocker…
What’s the future for derelict GRP boats?
With 9,000 GRP boats abandoned in Europe each year, finding disposal solutions isn't easy. Could new technologies be the answer?…
Even at this sharp end of the composite business, rapid advances are being made – driven by aerospace and Formula One.
‘We can now take away the expensive autoclaves and ovens – they can cure at ambient or 40-60ºC,’ says Ashley Parkinson, a research engineer with the UK National Composites Centre.
‘It’s a more expensive process to use, but in the high-performance market, it’s worth it.’
Greener composites
Now, there is nothing particularly sustainable about producing glassfibre – a technique that involves heating raw silica to 1,370º C, then pultruding the molten strands onto a bobbin.
You can use some recycled glass to lower your emissions, but it is an energy intensive process and it is very hard to extract the raw materials from end-of-life fibreglass.
Swiss supplier Bcomp tested alternative natural fibres 10 years ago, when it was a start-up in a garage.
‘Flax turned out to be the best in terms of mechanical properties, soil usage, water requirements and overall performance,’ explains marine and industry manager Paolo Dassi.
It actually locks up carbon rather than producing it – as much as 500g of CO2 per kilogram of flax.
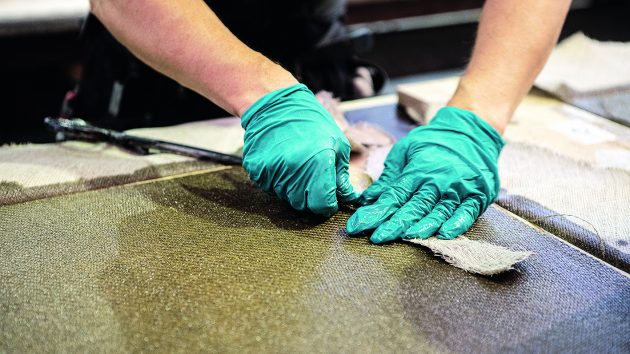
Precise cutting is key to reducing fibre wastage in boat building
‘The plant acts as a CO2 sink during its growth. This completely offsets the CO2 emissions of the manufacturing stages.’
Bcomp’s extraordinary growth began when it managed to process the flax stems to be of uniform size and flatness, replicating the grades possible using glassfibre.
Its AmpliTex product is available as a unidirectional, stitched biaxial or woven twill, ranging from 200-500gsm.
In lamination it is 50% stiffer than glass and just a little weaker, making it an ideal substitute.
Couple this with an extra flax mesh called PowerRibs, and you end up with a composite that closely resembles carbon, but with just 25% of the emissions.
AmpliTex has already been used in niche boat building projects, including the glorious Flax 27 daysailer by Green Boats of Bremen, which sports cork decking.
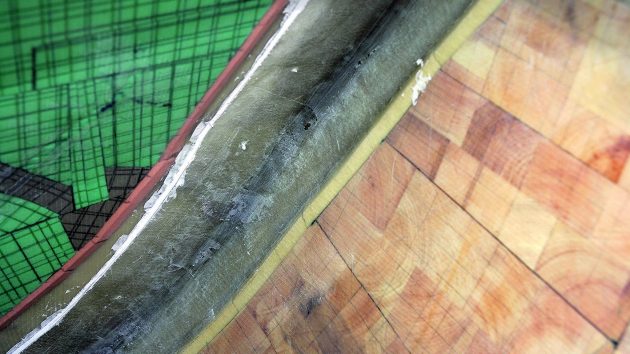
Foam sandwich hull construction (green) or balsa core (wood) is much stronger, for little extra weight. Credit: Graham Snook/Yachting Monthly
It was a key part of the lay-up of the new Café Racer 68 from Baltic. Although her hull is in carbon, 50% of the structural members were in flax composite.
France’s Windelo has taken a different tack in its catamarans.
It uses basalt fibre – made from melted volcanic rock – which ‘is slightly stronger than E-glass and just one-10th as carbon intensive to produce and use’.
Its first 50-footer has a hull that also features a recycled PET foam core for strength and stiffness. But it is not just the fibre that is being decarbonised.
So-called ‘green epoxies’ have been developed, where a significant chunk of the synthetic oil-derived molecules of the resin are replaced by bio-sourced molecules.
Gurit’s Ampro for hand laminating is 40% bio derived, for instance.
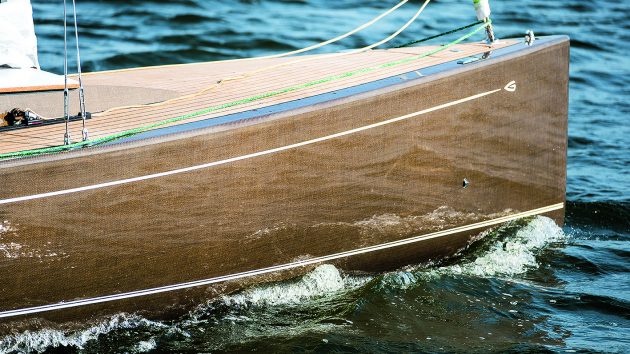
Green Yachts focuses on environmentally-friendly boat building techniques. Its Flax 27 is built of sustainable flax fibre
And the ProSet range from West Systems includes epoxies containing up to 30% bio molecules.
They can essentially just be dropped into any process that would have been suitable for the equivalent synthetic resin.
‘Any customer that is familiar with epoxy processing, vacuum consolidation or post curing will be very familiar with the process,’ says David Johnson of Wessex Resins, European manufacturer for West.
‘Even wet lay-up with no vacuum bagging.’
There is a modest cost increase, but it amounts to less than 25% compared to a standard epoxy, and a drop in the ocean of the boat’s overall build.
‘Bio-based epoxies are more expensive because there’s more sophisticated chemistry involved,’ says Johnson.
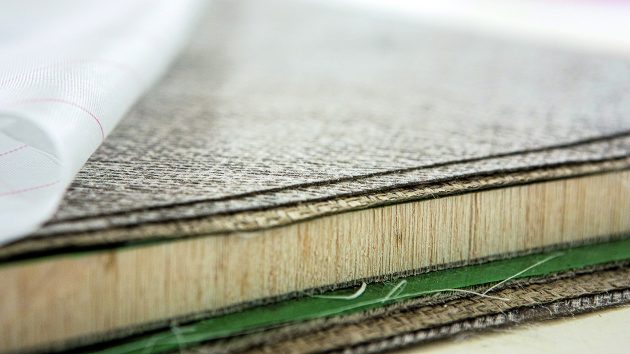
Pre-preg flax fibres being laid up around a balsa core
‘Compared to building a boat in vinylester or polyester, you can use slightly less material because of the superior qualities of epoxy. The end cost differences are negligible and there are benefits in lighter weight: you become more efficient, and the loads are less.’
Suppliers like Gurit are also finding ways to substitute the synthetic foam core used in sandwich hull construction.
Standard foam is made of virgin PVC, with all the associated environmental pitfalls.
Gurit has developed more renewable alternatives using up to 100% recycled PVC and balsa wood.
Builders from Arcona and X-Yachts to Bali and Gunboat catamarans use foam cores in their lay-up to build boats that are stiffer and lighter than they would be otherwise.
Away from composites
Some innovative new boat builders are going in another direction altogether, eschewing the by-now traditional GRP for something that can be genuinely reused repeatedly.
Start-up Vaan is building its 42ft R4 catamaran out of a grade of aluminium alloy commonly used in window frames and road signs, so up to 60% of the hull is already recycled.
‘There’s no way to distinguish it from virgin material,’ says Vaan founder Igor Kluin.
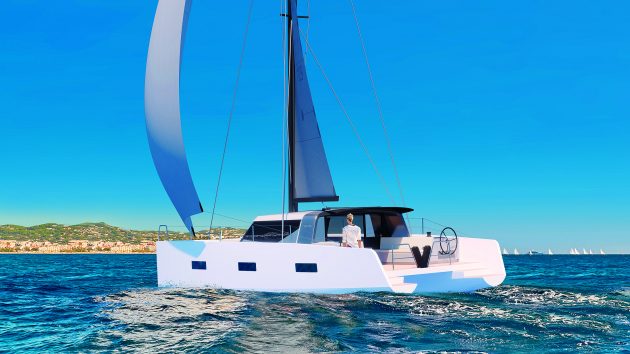
Vaan uses a high proportion of recycled aluminium to build its hulls, which can then be easily recycled
It hasn’t been easy to secure supplies, however. That’s partly because window frames last for 50 years or more and also competition with other sectors.
‘In the short term the costs are higher because there are so many people jumping on the bandwagon, but it has only 5% of the energy use of virgin alloy, so in the end it should be cheaper.’
Vaan’s novel approach to sourcing more sustainable materials extends to the interior finish as well.
It uses a pineapple leaf fabric instead of leather, plentiful European poplar for cabinetry, cork instead of teak decking and recycled PET.
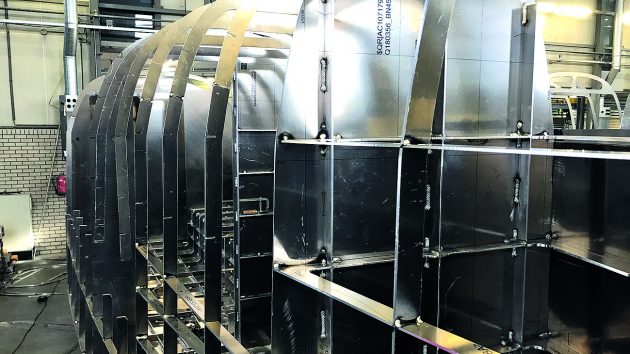
Greener boat building: A hull made from recycled aluminium
Parts of the boat are 3D printed – something that higher end brands are doing more and more of.
‘Recycled industrial PET is being 3D printed for the back of the Vaan spoiler because it produces a lower volume than moulding,’ says Kluin.
‘We want to see if it can become load bearing. We’re also 3D printing with aluminium, too. It’s useful for smaller structural elements that are hard to reach and would traditionally have been milled.’
Recyclability of boat building materials
Besides wood, all forms of composite suffer from the same problem; at end of life, it is very difficult to separate the component materials for re-use.
This is why using materials such as steel or aluminium can make sense, despite the higher environmental cost of the virgin metal. They can be reused repeatedly.
The composite recycling systems developed to date, which include pyrolysis, burning and shredding, are all unsatisfactory because of the energy intensity of the processes or the fact they yield a lower quality material that has to be downcycled.
In principle, it is possible to use resins that melt again at high temperatures and can be collected, refined and reused.
Elium resin from Arkema is capable of exactly that, and is already being used in recyclable wind turbine blades.
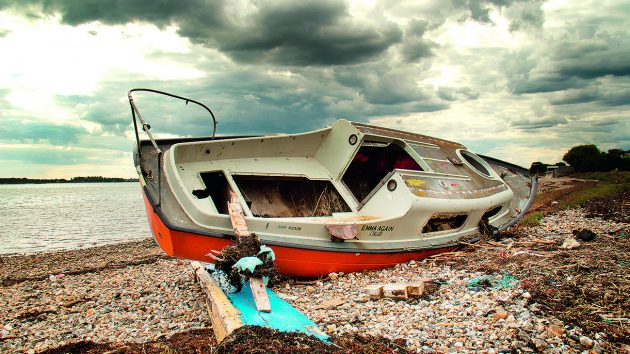
Laminate are expensive to separate for re-use. Credit: Rob Wilkinson/Alamy Stock Photo
They even built a 6.50m Mini Transat boat from it.
The process also yields reusable glass, but carbon and flax don’t support the heat: carbon loses as much as two-thirds of its strength and flax simply combusts.
However, an Australian study has shown how carbon-fibre composite can first be heated without oxygen in a pyrolysis chamber to burn off resin, then oxidised to yield carbon-fibre with most of the strength of virgin fibre but only 10% of the environmental impact.
Cured laminates can also be separated using a chemical process proven in the lab at the National Composites Centre, with a big vat of acetic acid.
Portsmouth University is researching enzymes to decompose plastic, starting with plastic bags.
The approach could eventually handle boats as well.
‘You have to find the right enzyme that works for snipping the molecules of a particular polymer. Practically, it’s a decade away,’ says Ashley Parkinson of the NCC.